Automation project
New skills learned
Conclusions and future work
Transporting materials with mobile robotics
Project context
First year of college and we are faced with a challenge in the subject of Project RII 1: Organization and Scenarios, the challenge consists of making a realistic automation proposal.
The proposal should improve the current manufacturing process of chargers for electric vehicles, which is developed by the company Power Electronics.
The problem to be addressed is the transportation of components and materials in the assembly area of the chargers.
Project deliverables
📋 Business case
The current problem of manual transport, which causes loss of time and fatigue in operators, is described and a solution is proposed using autonomous vehicles. The expected benefits are analysed, such as the reduction of errors and increased production, and a cost-benefit analysis is presented that justifies the initial investment and projects long-term benefits.
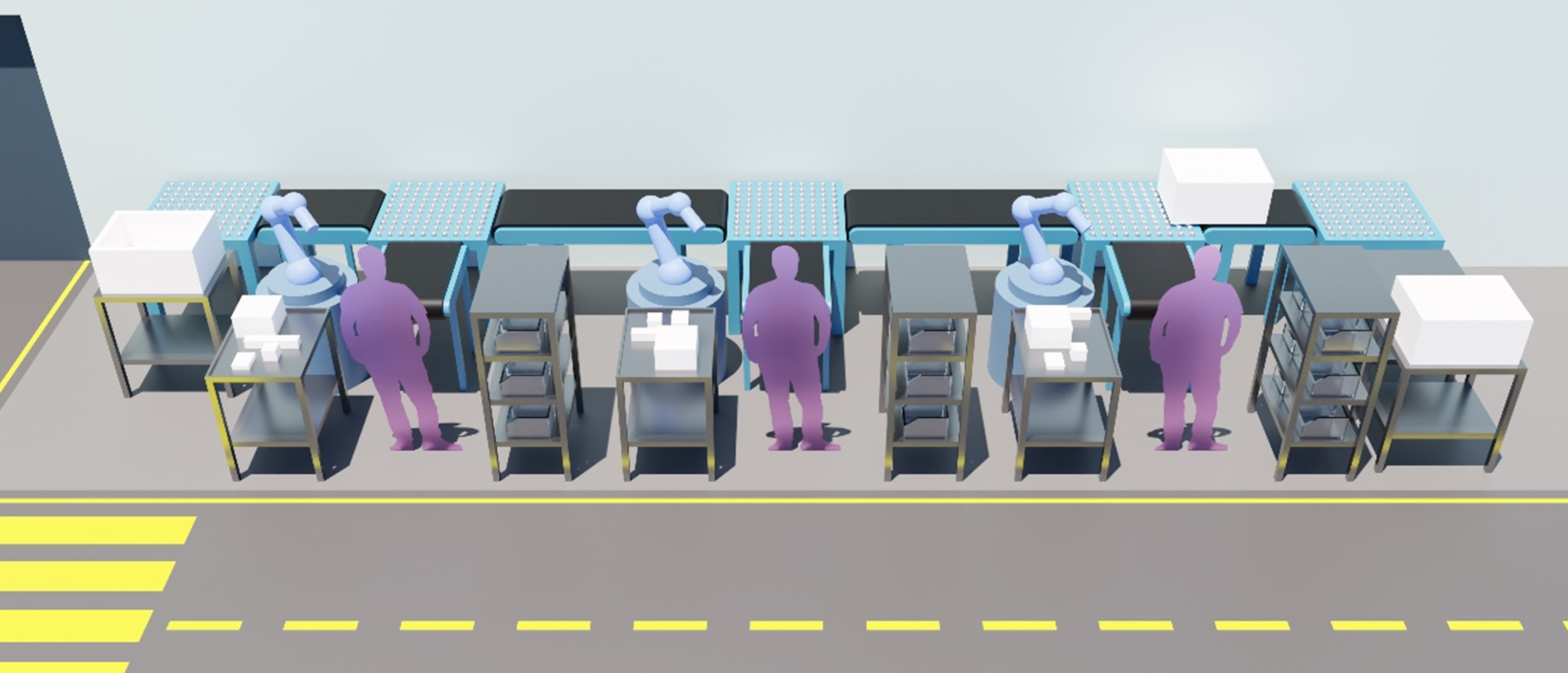
📝 Description of the process to be automated
Currently at Power Electronics, materials and components are transported manually using mobile tables pushed by operators. The proposal suggests the use of autonomous mobile robots (AMR) to perform these tasks, which would reduce production time and worker fatigue. Production times, materials and devices required are detailed, and the use of two AMRs is justified to optimize transport in the factory.
📖 Project Management Manual
It describes team structure, objectives, project scope, deliverables, and project planning, including the use of tools such as Gantt charts. It also addresses cost and risk management, highlighting the importance of staff training and ongoing monitoring to ensure project success.
The proposal
Power Electronics is proposed to use automated transport vehicles to replace workers pushing mobile tables for transporting materials and small chargers.
These robots would be responsible for picking up the shelves loaded with heavy materials and the unassembled chargers and taking them to the work area. They would also be responsible for transporting the assembled chargers to the inspection area.
a
🗒️ List of devices and technical budget
The necessary equipment is described, such as the RB-1 Base mobile robots and LiFePo4 batteries, as well as mobile tables for transporting materials. In addition, the costs associated with the training, installation and maintenance of these devices are detailed, estimating a total cost of approximately €60,000 for the implementation of the project. A joint budget with another assembly automation project is also mentioned, highlighting the synergy between the two.
💡 Automation proposal
Autonomous mobile robots (AMRs) are being considered to replace workers in the task of pushing mobile material transport tables and small chargers. Automation aims to improve efficiency and reduce staff fatigue, allowing workers to focus on more productive tasks. AMRs will communicate with workers via a mobile app and will be easily integrated into existing infrastructure, with minimal modifications required.
📏 Rules and regulations
The importance of complying with the ISO 3691-4:2020 standard, which sets out the safety requirements for AMRs, is highlighted. In addition, various safety measures are mentioned, such as the use of photocells, bumpers, acoustic and light warning systems, and emergency stop buttons. The risks associated with the use of AMRs, such as collisions and contact with battery acids, are also addressed and preventive measures are proposed to mitigate them, including the delimitation of transit areas and staff training.
New skills learned
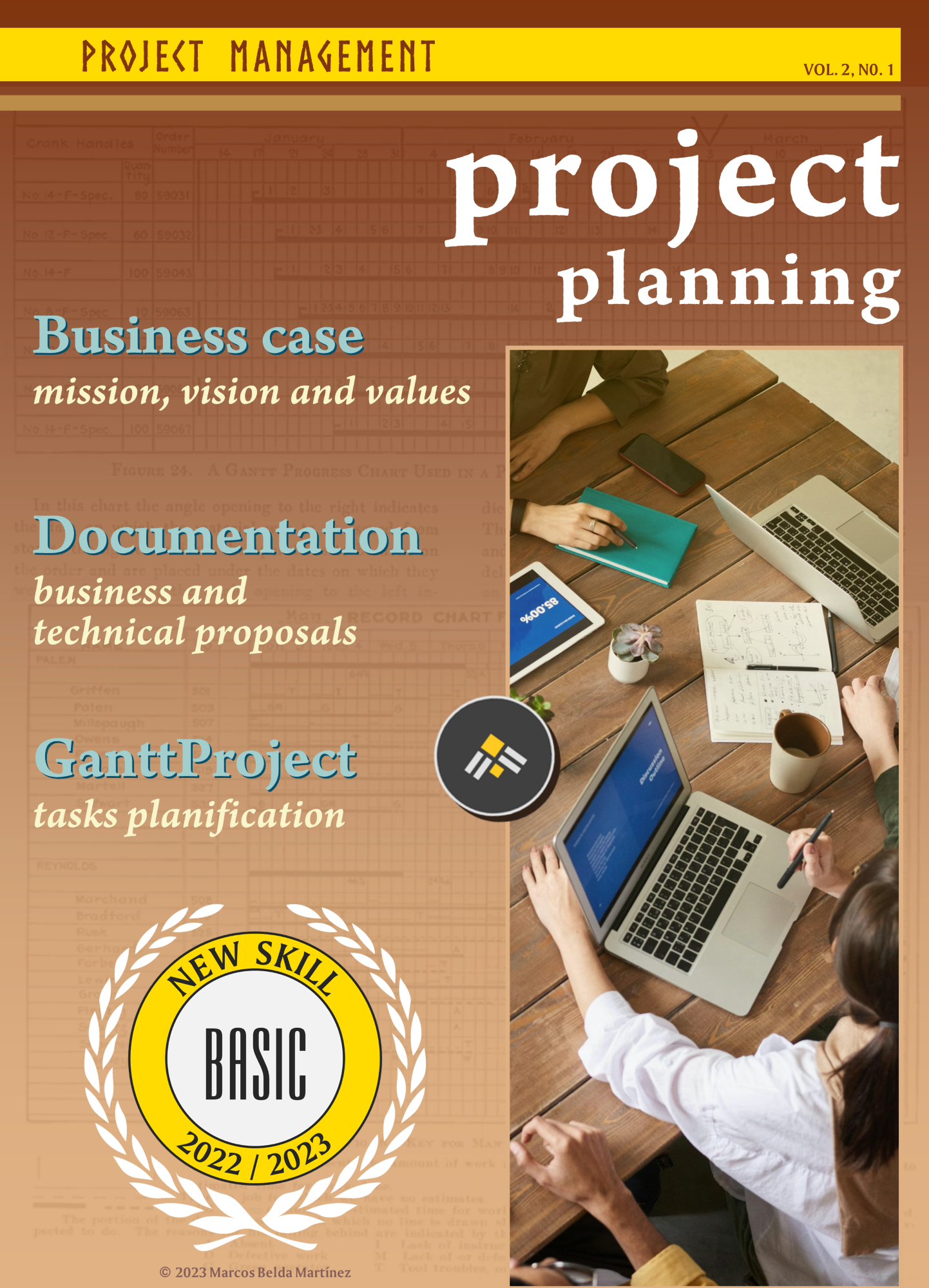
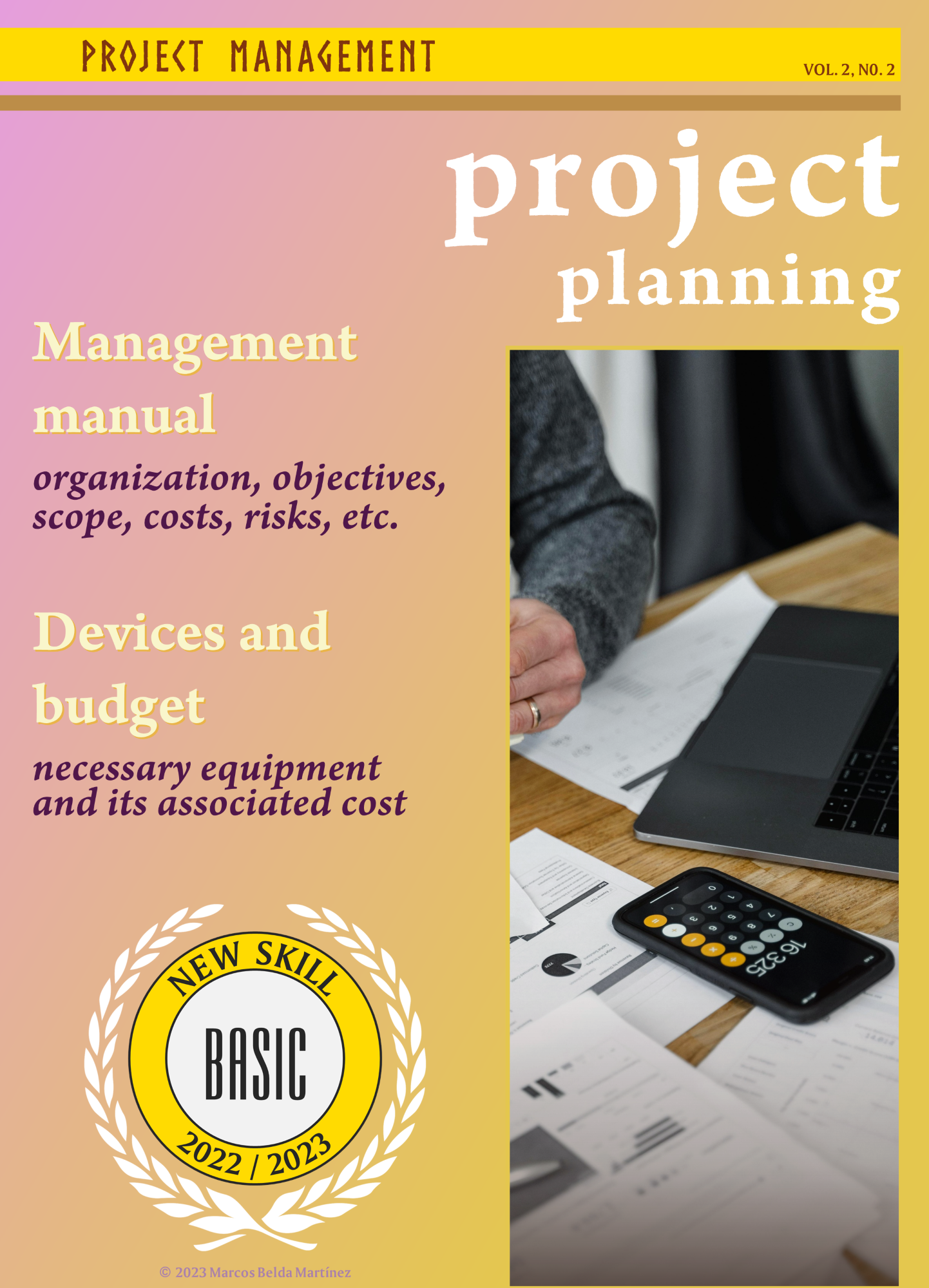
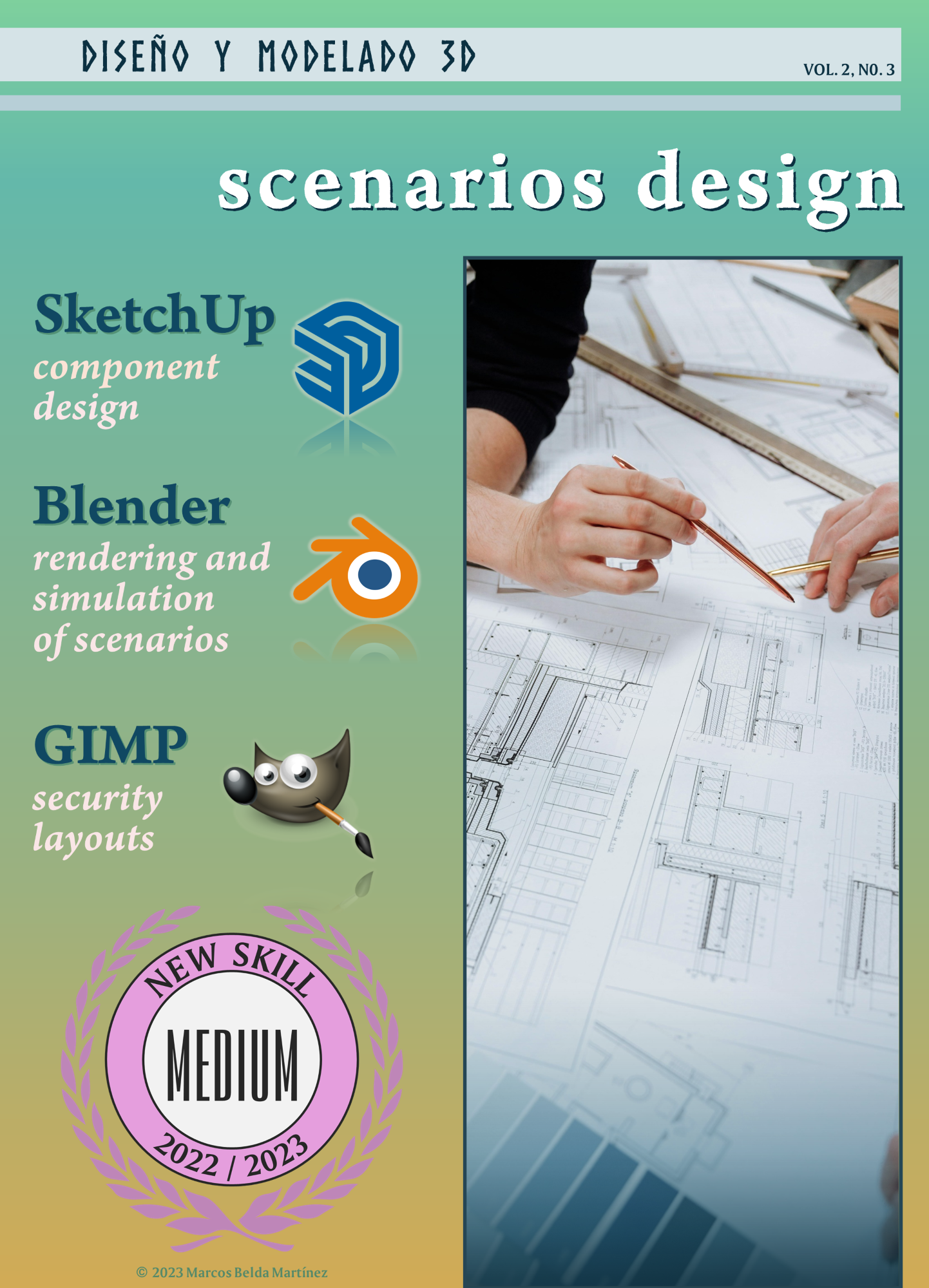
Conclusions and future work
The completion of this project has provided us with new knowledge both on a personal and professional level. We have learned to work as a team, manage projects and apply theoretical knowledge to practical situations.
The implementation of autonomous mobile robots (AMR) in the material transportation process at Power Electronics has proven to be a viable and beneficial solution.
Special thanks
This project would not have been possible without the help of the Fundamentals of Business Organization teachers and Eduardo Vendrell, professor of the subject RII Project 1: Organization and Scenarios. It is also worth mentioning the work of coworkers Carla Hidalgo and Lourdes Francés.
Main conclusions of the project
- Reducing fatigue: AMRs have significantly reduced the physical burden on operators, allowing them to focus on more productive tasks.
- Increased efficiency: Automation has optimized production times, reducing errors and improving the quality of work.
- Return on investment: The cost-benefit analysis has shown that the initial investment will be recovered within a reasonable period of time, with long-term benefits.
Future work
- Staff training: Continue employee training to ensure smooth and efficient integration of AMRs into the work environment.
- Project expansion: Consider implementing AMR in other areas of the factory to maximize benefits.
- Continuous improvement: Continually evaluate and update systems and processes to adapt to new technologies and needs.